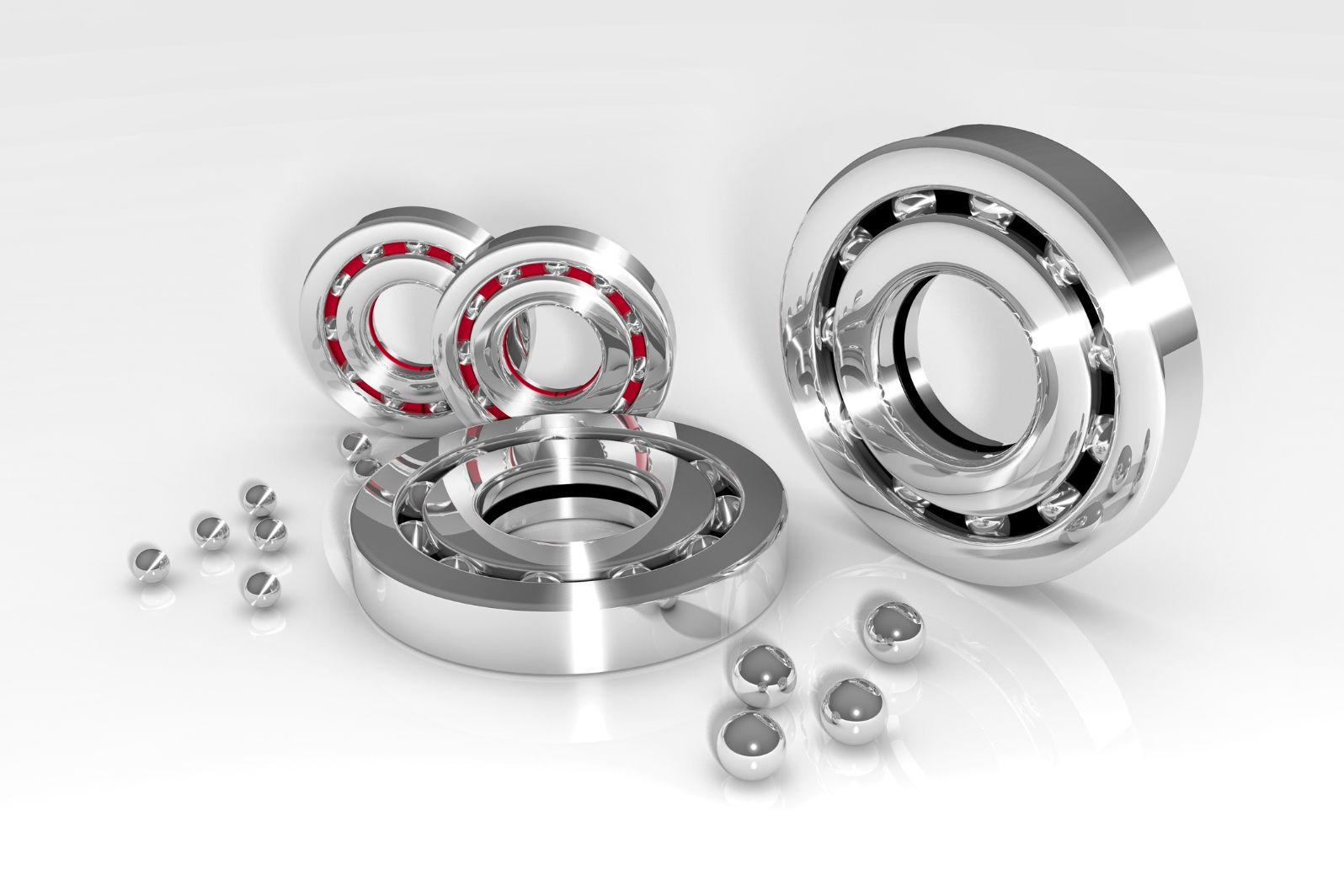
The significance of seals and bearings in the world of machinery and industrial equipment cannot be overstated. These apparently little parts assume a critical part in guaranteeing smooth tasks and forestalling expensive breakdowns. Seal and bearing optimization has never been more important as industries continue to push the limits of productivity and efficiency. Elevate your machinery’s potential with next-generation seal and bearing services by Eclipse Engineering, also redefine the performance and reliability
The Foundation of Efficiency
Seals and bearings are the unsung heroes that silently work behind the scenes to keep our factories running, our vehicles moving, and our appliances functioning. Bearings, whether roller bearings, ball bearings, or plain bearings, facilitate rotational or linear movement by reducing friction and enabling smooth motion between two moving parts. Seals, on the other hand, act as barriers, preventing contamination from entering and lubricants from escaping critical components.
The efficiency of machinery is directly linked to the performance of these components. Any degradation in their function can lead to increased friction, overheating, energy inefficiency, and even catastrophic failures. This is where seal and bearing optimization comes into play.
Challenges in Seal and Bearing Performance
Industrial environments are harsh and demanding. Seals and bearings must endure a myriad of challenges, from high temperatures and heavy loads to exposure to corrosive substances. Over time, these conditions can lead to wear and tear, reducing their effectiveness and lifespan.
To address these challenges, engineers and researchers have been working tirelessly to develop advanced materials and designs that can withstand extreme conditions. For example, ceramic bearings are gaining popularity due to their high strength, heat resistance, and low friction properties. Similarly, elastomeric seals with specialized coatings are being developed to enhance their durability and chemical resistance.
Precision Engineering for Optimal Performance
Optimizing seals and bearings involves a combination of precision engineering and innovative materials. Engineers carefully analyze factors such as load distribution, operating speeds, temperature variations, and lubrication methods to design components that can perform optimally under specific conditions.
One of the key approaches to seal and bearing optimization is predictive maintenance. Through data collection and analysis, engineers can monitor the condition of these components in real time, allowing them to identify early signs of degradation or malfunction. This proactive approach enables maintenance teams to schedule replacements or repairs before a catastrophic failure occurs, minimizing downtime and maximizing overall productivity.
The Road Ahead
As technology continues to advance, the future of seal and bearing optimization holds exciting possibilities. The integration of sensors and IoT (Internet of Things) technology into these components could enable real-time monitoring on a scale never seen before. Imagine a factory where every bearing and seal communicates its performance data to a central system, allowing for predictive maintenance on an unprecedented level.
In conclusion, seal and bearing enhancement isn’t just about broadening the life expectancy of parts; It’s about improving the sustainability, dependability, and efficiency of all industries. Together, these seemingly insignificant factors shape the modern manufacturing and infrastructure landscape. As we keep on investigating new boondocks, the excursion towards expanding the life expectancy and execution of seals and course stays a fundamental piece of the mechanical development.